PEKK Laser Sintering
High-performance additive manufacturing

Three-dimensional printing of high-performance thermoplastic materials such as PEEK, PEKK and ULTEM (PEI) is something that has become widely popular in recent years, mainly thanks to FDM technology.
The maturity of a relatively simple technology, coupled with the possibility of achieving very high temperatures during the extrusion / material deposition phase, are two of the key factors that have enabled the emergence and expansion of an industry – that of 3D printing of high-performance components – in a relatively short time.
As everyone knows, each technology has its pros and cons, and we will look at some of the differences between FDM (also called FFF) and laser sintering technology below.
SLS vs FDM 3D printing
Speaking of printers operating at standard temperatures (around 200/210 °C), despite a higher average hardware cost, the advantages of SLS technology over FDM technology are many:
-
Higher printing speed
Not really linked to the amounts of parts to be printed -
The possibility to exploit the entire available volume
-
The fact that no supports have to be printed
-
A higher printing resolution
For finer details -
Generally better and more isotropic mechanical properties
-
The possibility to print more complex geometries
But in spite of all these advantages, and in spite of the fact that SLS printing of PEKK is something that has been available for a few years now, it is undeniable that for the time being the most popular technology in this field remains FDM, mainly due to lower costs, and the possibility to print large parts with relative ease.
What is limiting the adoption of SLS PEKK 3D printing?
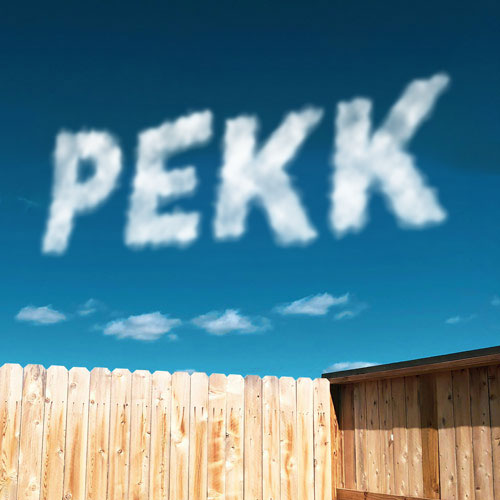
One of the biggest barriers to the adoption of new technologies has always been the economic factor.
A standard SLS printer, and often for good reasons, costs on average tens of times more than an FDM equivalent, and the same is true for high-temperature laser sintering printers, making the initial investment prohibitive for many research centres and OEMs.
Add to this the cost of the powder itself, and the fact that the only SLS printers capable of printing PEKK currently have volumes well above 80 litres, and it is easy to understand why most users opt for FDM solutions.
These are exactly the insights that prompted us to start the STROM project.
Advantages of making a technology
available to a wider audience
At Verne, we firmly believe in the importance of spreading knowledge and technology, engines of innovation.
The Strom project was born precisely with the aim of democratising the adoption of high performance SLS printing, through the development of a printer with first-class features and print volumes compatible with those required by laboratories, research centres and OEMs.
The advantages of the Strom project can be summarised with:
-
Initial investment reduced by several orders of magnitude compared to currently available systems
-
Reduced print volumes allowing more efficient use of the platform
-
Open parameters, allowing research centres to explore
-
Accelerated time-to-market of printed parts
-
Possibility to create dedicated printing services with high scalability and efficiency
-
Accelerating innovation in the medical, aerospace, automotive and energy fields
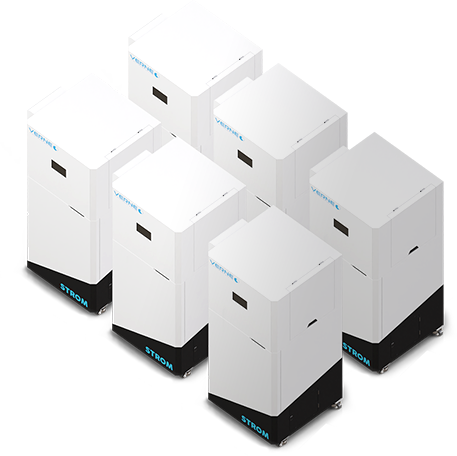
Polyetherketoneketone (PEKK) application fields
PEKK’s outstanding mechanical, chemical and thermal properties makes it the ideal for sectors where performance is a crucial requirement.
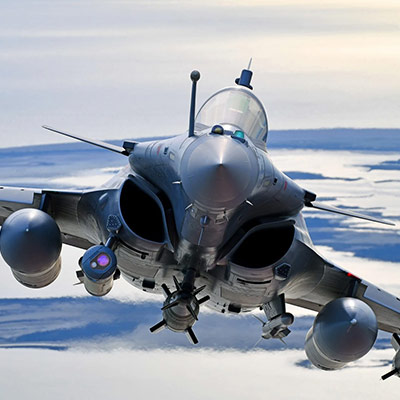
Aerospace and defense
High temperature resistance, lightness, chemical resistance and dimensional stability
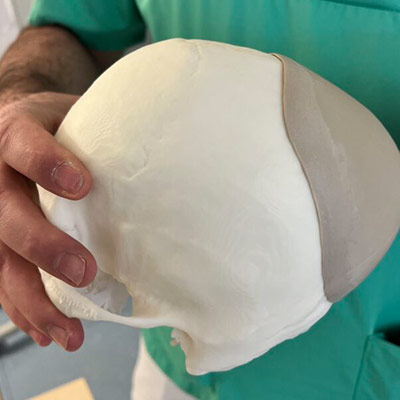
Medical
Biocompatibility, radiolucency, wear resistance, lightness
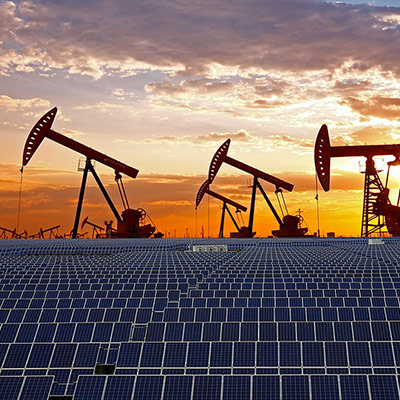
Oil and energy
Resistance to aggressive chemicals, corrosion resistance and robustness, wear and fatigue resistance
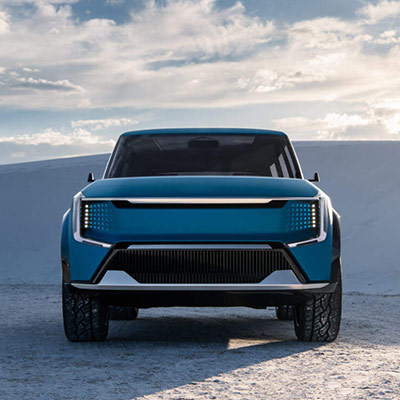
Automotive & electronics
Resistance to high temperatures, chemical resistance and lightness
Performance in numbers: PEKK vs ULTEM
Ultem is one of the most renowned choices when it comes to additive manufacturing with high-performance thermoplastics, so we think that a one-to-one comparison with SLS printed PEKK can serve as an interesting reference.
Test | FDM Printed Ultem value | SLS Printed PEKK value | UoM |
---|---|---|---|
Specific Gravity, 73°F | 1.28 | 1.39 | - |
Tensile Strength X,Y @ Yield, 73°F | 9300 | 11603 | psi |
Tensile Strength Z axis @ Yield, 73°F | 5990 | 8847 | psi |
Tensile Modulus of Elasticity, 73°F | 401 | 942 | psi |
Flexural Strength X,Y, 73°F | 21000 | 14649 | psi |
Flexural Strength Z axis, 73°F | 11100 | 11784 | psi |
Flexural Modulus of Elasticity | 500000 | 86500 | psi |
Melting Point (Crystalline) Peak | 627 | 575 | °F |